Maintaining
The Thermal Balance Core To Cavity: The Key To Cooling Efficiency
Dr. Paul Engelmann and Eric Dawkins
Department of Industrial and Manufacturing Engineering
Western Michigan University, Kalamazoo, MI
Michael Monfore, Ralston Foods, Battle Creek, MI |
Abstract |
Achieving parts with
maximum dimensional stability coupled with minimum cycle times, is a goal of most molders.
Previous studies have shown that a majority of heat contained in the molded part is
removed through the core of a mold. Application of high strength, high thermal
conductivity copper alloys to core, cavity, and gate areas, has led to some revelations.
These data shed new light on the effect of change in temperature vs. change in thermal
conductivity. |
Background and
Introduction |
A thorough understanding of
where greater heat removal can improve the dimensional stability of a part is an important
step in the quest for zero defect products. Research into the effects of applying high
strength, high thermal conductivity copper alloys to injection molds has been underway
since 1995 at Western Michigan University (WMU). Researchers gathered non-structured
anecdotal information about the experiences various professionals in the plastics industry
had with applying copper alloys to injection molds. Although the majority of
experiences related to the research team were positive, those people with most extensive
experience reported times where application of copper alloys were not always effective in
reducing part warpage or cycle time. Although this response represented a small fraction,
it nevertheless raised the question about whether high thermal conductivity was
necessarily better for all applications. Early studies focused on use of copper alloys
for the core section of a mold (1). Application of both normally watered copper cores and
non-watered copper cores attached to watered copper chill plates has been shown to
significantly improve the dimensional stability and cycle time required to mold a given
part (2). The other logical piece of this investigation was to determine the effect
of applying copper alloys to the cavity side of the mold. As the majority of non-favorable
anecdotal experiences related to cavity applications of high thermal conductivity alloys.
It was decided that a thorough investigation should be undertaken to determine the range
of effects that high thermal conductivity materials had dependent upon the processing
strategy.
Cooling analysis predicted that a majority of heat Load was given up through core-like
structures in the mold.
That is to say that a positive structure, or core, tended to have a higher
heat load per unit of mass. This was most pronounced when the part shrunk onto the core,
thus losing surface contact with the cavity. Instrumented studies on the test tool at WMU
confirmed that a majority of the temperature swing, and thus the heat removal, was
proceeding through the core of this tool (3). It was decided the relationship between core
material and cavity material needed to be investigated. Since the submarine, or tunnel
gate, was located in the cavity section of the tool, the relationship between cavity
material, gate size, and cavity temperature also needed investigation. This was based upon
the hypothesis that a higher thermal conductivity alloy could cause premature gate freeze
and therefore compromise the processors' ability to pack out me part. Inability to
pack the part could result in both dimensional changes and an increase in defects such as
sink. |
Experimental Design |
The study utilized an
incomplete block design in which the various cavity/core treatments were applied over a
sequence of equally spaced cycle times. The set of cycle times used, shifted as
appropriate for each treatment combination. This shift conserved resources while
still allowing the key responses to be measured for each treatment group. This strategy
enabled the research team to review various gate sizes between .81 mm (.032") and 97
mm (.038"). Gate inserts were produced out of both type 420 SS and C18000 as a
representative copper alloy. In addition, a series of mold cooling temperatures were
selected. Water temperatures ranged from 100 C (500 F) to 660 C (1500 F). The mold used for the experiment was a 33 mm bottle cap mold
with interchangeable cores and core mounting plates with a spiral baffle in the cores. The
resin used was a Huntsman polypropylene copolymer. All work was done on a VanDorn 77
metric ton (85-ton) hydraulic toggle injection molding. The injection screw was a 35 mm (1
3/8" diameter) with a 20.6 cc (5 ounce) shot. Mold water was regulated by a AEC mold
temperature controller and a 2.7 metric ton (3-ton) Thermal Care chiller. Circuit water
was monitored on all zones for flow rate, input and output temperatures, and pressure loss
through the circuit. Cavity pressure, screw position, and hydraulic pressure were
monitored by an RJG Technologies DART system. Thermocouples in the cores were embedded in
heat transfer compound eliminating air gaps to read more accurate temperatures.
The thermocouples were connected to an analog input computer card. Readings were
processed with Strawberry Tree's Quicklog PC data acquisition & control software.
The parts were allowed to stabilize in a testing lab under ASTM
environment guidelines for a minimum of 96 hours. A gage was constructed to measure part
warpage. Part warpage was determined by the amount of deflection across the surface of the
bottle cap. A measurement was first taken along the edge height of the bottle cap with a
digital plunger indicator. Another measurement was then taken at the center of the bottle
cap. The center measurement was then subtracted from the edge measurement in order
to determine warpage. Gage repeatability and reproducibility (R&R) was done using a
standard ANOVA method. |
Findings |
Examination of various core
and cavity combinations yielded the following information about the relationship of copper
alloys to their position in the mold. All of the baseline copper alloy core data
were drawn from experiments using a type 420 SS cavity. It was expected that substituting
copper for the stainless steel cavities would improve performance with the various copper
cores. Figure 1 compares the effect of substituting C17200 and type 420 SS cavities
while maintaining a C18000 core. In addition, the data for type 420 SS cavity and core was
included as a reference comparison to standard practice. It can be
observed from this graph that the type 420 SS cavity using the C18000 core, had the most
uniform performance and provided acceptable parts at a faster cycle than any of the other
combinations. The line for the C17200 core using a C18000 cavity began at a
shorter cycle time due to the faster gate seal with a copper cavity
It is interesting to note that the final warpage in parts produced by the
C17200 cavity with a C18000 core was the same as those from the type 420SS cavity with a
C18000 core. Since the gate was located in the copper cavities, it froze approximately two
seconds faster than the gate located in the steel cavity.
A premise of this study was that even though it is sometimes done as industrial
practice, parts should not be ejected prior to gate seal. Therefore, the shortest possible
cycle for the C18000 core, type 420 SS cavity was completely dictated by the gate freeze
time using the steel cavity. It was, therefore, logical to assume that although
parts may have been of diminished quality, they could have been ejected in less than 7.3
seconds using the type 420 SS cavity in combination with the C18000 core.
Figure 2 demonstrates that the amount of warpage in the final part, is dependent upon
the cavity material. In this example, the C18000 cavity using either C17200 or
C18000 cores produces more warpage than the type 420 SS cavity with either copper alloy
core.
As was previously noted, the parts molded using the C18000 cavity were able
to be ejected earlier than those parts molded using steel cavity due to gate freeze times.
The ideal cooling curve would be shallow and have the smallest minimum warpage in the
final product.
It may be noted in Figure 3 that the slope and general configuration of matched alloy
core and cavity sets was very similar. The shape of the cooling curve produced, using a
copper core and a copper cavity, was very much like the shape of the cooling curve using a
steel core in conjunction with a steel cavity.
It may be noted here that both the final warpage achieved and length of rime required
before solidification allowed ejection of the part did differ. In this case, parts
produced with a C18000 core and cavity were ejectable at 5.2 seconds. However, their
warpage did nor stabilize until roughly 7.2 seconds. Parts produced using the type 420 SS
core and cavity could not be ejected until 7.2 seconds and those parts did not stabilize
until 9.2 seconds. In addition, when the differential was reversed by using a steel core
and a C18000 cavity the poorest overall warpage curve was achieved.
Comparison with the optimum type 420 cavity and C18000 core demonstrates the profound
affect of higher thermal conductivity in the core. Therefore, the shape of the
cooling curve appears to be dependent upon the differential, or lack thereof, between the
cooling rates offered by the core and cavity.
It was theorized that in order to favorably alter the heat removal between core and
cavity of the same material, that the core and cavity should be run at different
temperatures. Figure 4 graphically illustrates what happens as the cavity temperature was
raise while holding the core water temperature uniform. Using a C18000 core and cavity,
the water temperature of the cavity was raised in increments of 100C
(500 F). This produced interesting results. Although the
three curves are similar in shape, it is interesting to note that the curve using a 100 C to core water and 660 C (1500 F) cavity water shows a more pronounced step in the curve.
This directly relates to the glass transition temperature of polypropylene. In
other words, raising the cavity temperature not only made the cycle longer but also
probably increased the crystallinity in the resulting parts.
It was also suggested the part warpage phenomenon might in fact be influenced by gate
size. Therefore, gate diameters of .81 mm (.032") through .97 mm
(.038") were used. This range of testing represented a 41% increase in total area to
be solidified. Yet, the resulting cooling curves in Figure 5 are virtually identical. It
was expected the .97 mm (.038") gate should have stayed open longer prior to gate
freeze than the .81 mm (.032") gate and that this should yielded a better packed
part. Thus, achieving a lower overall warpage baseline. Notice that although there were
some very minor differences in the curve itself, there was no discernible difference in
the baseline whatsoever.
The other proposed method of altering gate freeze was the use of a
stainless steel gate insert. Since the gate insert represented the top of the runner,
gate, and a section of the side wall, it was proposed that a stainless steel gate insert
should produce a long gate freeze time. Again, allowing for additional packing of the
part. Figure 6 illustrates the C18000 cavity with C18000 core using gate inserts of
stainless steel and C18000 copper. Both gates were identically sized at .97 mm
(.038") in diameter. Figure 6 shows that there was no appreciable difference either
in the baseline or in the solidification curve with this modification. |
Conclusions
and Recommendations |
The data presented here
leads one to the following understanding. First, for this mold, the primary factor that
affected warpage was the heat removal from the cavity vs. the core of the mold. This is
not surprising as it has been supported by numerous other studies. However, there are a
series of important nuances. These data show that a thermal differential between the
cavity and the core is important. In the past, it had been suggested that simply heating
up the cavity side of the mold might accomplish the same thing. However, these data
clearly indicate that running the cavity hotter than the core only lengthened the cycle
time, and made the part warpage more pronounced.
Probably the most complicated decision is how to achieve the thermal balance. The
copper core, with a steel cavity, clearly produced parts with minimum warpage in the least
cycle time. However, use of a copper cavity did achieve a faster gate seal.
Therefore, if part warpage is not a significant consideration, using a copper cavity with
a copper core could allow recovery of the injection unit sooner, than with any other
combination.
In addition, when lower thermal conductivity C17200 was used for a cavity. and higher
thermal conductivity C18000 was used for the core, low final net warpage is
achieved. In fact, the C17200/C18000 combination yields the same
final warpage as the optimum C18000 core using a type 420 SS cavity. In a large volume
part, this might allow an earlier recovery of the screw, which could in fact lead to an
overall shorter cycle.
It is also reasonable to assume that since C17510 and C18000 have very similar thermal
conductivities, that a C17510 core and a C17200 cavity should behave similarly to the
C18000 core with the C17200 cavity.
It is important to note that applying a copper cavity with a steel core throws the
thermal balance in the wrong direction. This situation should be avoided as it does not
afford any benefit either to the part quality or cycle time. However. a core-like
structure, on the cavity side of the mold, would behave as score, not as a cavity.
In each situation, it is important to assess what type of structure is in the mold
rather than which side of the mold the structure occurs on. Cooling analysis is therefore,
an important piece of overall cooling design. The more complicated the core to cavity
structures are, the more difficult it will be to maintain the thermal balance without
using some method of verification.
It is the recommendation of the research team that core-like
structures be made of high thermal conductivity, high strength
copper alloys, unless something about a given mold design defies their use. In other
words, it is time to start asking why a core structure is not made out of a high strength
high thermal conductivity copper alloy rather than asking if it is an option that should
be considered. |
Acknowledgments |
The research team at
Western Michigan University wishes to acknowledge the significant support of a number of
organizations and individuals. The Copper Development Association Inc. for providing the
financial support for this research. Performance Alloys & Services Inc., Brush
Wellman Inc., Copper and Brass Sales, and NGK Metals provided alloys for the mold. Research assistance was also provided by Bob Dealey,
Cliff Moberg, Dr. Dale Peters, Jay Shoemaker and Scott Smyers.
These students put in many hours: Tom Bayer, Ole Hansen, Jerome Hund, Pat Jeakle,
Eric Peterson, Tim
Perkins, Frank Rinderspacher, Dennis Rosten. and Ryan Wejrowski |
References |
- Engelmann, P., Dawkins, E., Shoemaker, J., Monfore, M. (1996). Predicting the
performance of copper alloy mold cores. Plastics Engineering, vol. 52 (10), pp.
35-37.
- Engelmann, P., Dawkins, E., Dealey, R., & Monfore, M. (1998). Getting Heat out of
the Mold Where Water Won't Go. Technical Papers, vol. 44, pp. 836-840, Brookfield.
CT: SPE
- Engelmann, P., Dawkins, E.. Shoemaker. J., Monfore, M. (1997). Improved product quality
and cycle times using copper alloy mold cores. Journal of Injection Molding Technology,
vol. 1 (1), pp. 18-24.
|
KEY WORDS: mold, core, cavity, copper |
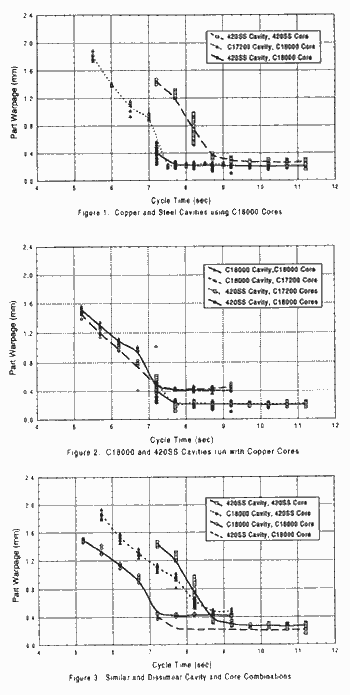 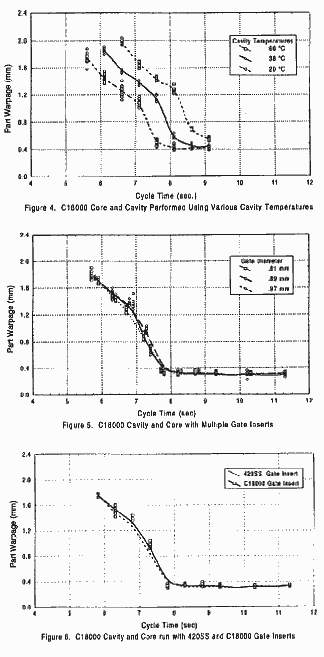 |
SITE INDEX
|
Disclaimer
While the information contained is deemed reliable, no warranties are expressed or
implied. For specific information regarding an application please call 1-800-272-3031 or
e-mail us at sales@moldstar.com
|
|
Copyright © 1998-2014 by Performance Alloys &
Services, Inc
Web site hosted by APLUS Hosting
All Rights Reserved.
|
|