Articles & News
|
Kodak cools cartridge cover with copper
alloy cores |
Every year
Eastman Kodak Co. molds hundreds of millions of 35-mm film canister covers, gray LDPE lids
well known to photographers. But a few years ago these covers were the cause of
headaches. Chronically hot cores were causing pulled centers where the part failed
to eject.
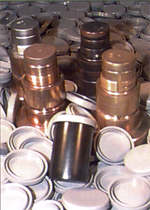 |
When Kodak wanted to improve
production and quality on these film canister covers, tooling material choice made a
significant difference. |
|
|
The steel used for the cores was a 420
stainless. Kodak thought it could run cooler and faster with a copper alloy core, but
before making the investment, decided to do some testing on the hypothesis.
The copper alloy Kodak tested is C18000, which according to specs, is nine times more
conductive than 420 stainless steel. However, C18000 is also softer, with a hardness of 92
to 94 Rockwell B, vs. 48 to 52 Rockwell C for the stainless steel.
Because of this, Kodak decided also to test three surface treatments to protect the cores
from gassing and plastic abrasion. Most 35-mm cover molds run for a year or more before
preventive maintenance is performed. |
Heat transfer values, in BTU |
Heat transfer |
420SS |
Copper Alloy |
through LDPE cover
through mold core |
2.44
1.40 |
2.63
4.01 |
Figure 1: Kodak's Lebeau and Glozer first
assessed the thermal conductivity of the stainless steel, copper alloy, and the LDPE cover
part. The results from this steady state test show that the cover generated heat at a
faster rate than the stainless could remove it. The copper alloy's thermal conductivity
should be able to cool the 35-mm cover faster. |
Thermal
Conductivity
The project was headed up by senior technical personnel Gary Glozer and Brett Lebeau, who
work at Kodak's Enterprise process and Tooling Development Lab in Rochester,. NY.
They started by assessing the conductivity of the stainless steel and copper alloy. Using
some relatively simple math, Glozer and Lebeau calculated the thermal conductivity of the
steel and alloy, as well as the LDPE material used in the part itself.
What they discovered was that the heat transfer value of the LDPE cover was greater than
the heat transfer value of the stainless steel mold core (Figure 1). This meant that
the current 420 stainless steel core could not take heat away as fast as the plastic
gave it up. On the other hand, the copper alloy showed its potential by removing heat one
and a half times faster than the; plastic gave it up. |
The
Single Cavity Test
A single-cavity 35-mm cover mold was built to production specifications and used for
initial lab testing. A copper alloy core and a stainless steel core were also fabricated
to production specs and interchanged within the single-cavity mold, run
in a 125-ton Farrel.
To start Glozer, and Lebeau installed the copper alloy core and
produced parts at seven different processing conditions. Process changes included mold
water temperature, water flow rate to the core and cavity, plastic melt temperature, hot
tip temperature, and part cooling time. Ten part temperatures at ejection were recorded
for each processing condition.
The entire process was repeated with the 420 stainless steel core
installed in the same tool. At all seven processing conditions the copper alloy core
produced substantially cooler parts than did the 420 stainless steel.
Differences in part temperatures produced by the two cores ranged from a low of 14 deg F
to a high of 24 deg F. On average, the copper alloy cores ran 18 deg F cooler than the 420
stainless steel cores. Encouraged by these results, Glozer and Lebeau decided to
scale the testing up to a 48-cavity production stack mold. |
The 48-Cavity Test
As mentioned earlier, the C18000 copper alloy is significantly "softer" than,
the 480 stainless steel. As part of the 48-cavity production trial, Glozer and
Lebeau also tested three different surface enhancements on the copper ally cores,
chrome, titanium nitride and boron carbide (carbon black). Of the 48 copper alloy cores,
three sets of 12 were treated with each coating. The fourth set of 12 was left untreated
as a control. The cores were distributed evenly though out both halves of the stack mold
to test the effect of core location on each surface treatment. |
Copper alloy vs. stainless steel |
Core
Material |
Average Temp.,
deg F |
Cycle Time,
Seconds |
420 SS
C18000
|
110
83
85
89
92
98
104 |
10.7
10.7
10.1
9.5
9.0
8.5
8.0 |
|
To start the
test, Glozer and Lebeau collected temperature data on the stainless steel cores. Their
results show the stainless steel produced parts on 10.7-second cycles with an average part
temperature of 110F. The mold was then removed from the machine --a 220-ton Husky-- and
the copper alloy cores were installed. The mold was reinstalled and run at the same
process conditions. for the same 10.7-second cycle, average part temperature from the
copper alloy cores was 83F. |
Encouraged by
such results, Glozer and Lebeau started reducing the cooling time on the process in
.5-second intervals. The most that could be taken off was 2.7 seconds, which allowed
for the fastest cycle of 8 seconds. This was dictated by the amount of time required for
screw recovery. As cycle time decreases, part ejection temperatures increased. |
Even at
the fastest cycle of 8 seconds, the copper alloy cores produced parts that were cooler
than those from the 420 stainless steel cores. |
However, even
at the fastest cycle of 8 seconds, the copper alloy cores produced parts that were cooler
than those from the 420 stainless steel cores. For production, Glozer and Lebeau
settled on a midrange cycle time, which they calculated would provide substantial savings
and eliminate the pulled core problem. This midrange cycle time also would most
likely provide the greatest margin of processing error.
Coating of Choice
The mold was in production for more than 30 weeks, ran 1.12 million cycles, and produced
more than 53 million parts, none of which was returned for pulled centers. Then the
durability of the surface treatment was assessed. As expected, the uncoated copper
alloy cores showed a visible change in appearance of the vapor-honed surface texture in
the area directly across from the gate. There was little coating left on the cores
protected with the boron carbide. It appeared the coating did not effectively adhere to
the copper alloy substrate and eventually wore off. Texture changes were similar to those
of the uncoated ones, but less severe. At $88 per core, the boron carbide was also the
most expensive coating.
The chrome-coated cores showed a slight visible change in appearance but there were no
signs of adhesion problems. The chrome was the least expensive at $8 per core. The
titanium nitrided cores revealed no visual change in appearance and outperformed even the
chrome. At $26 per core, the titanium nitride was deemed the best performer for the money
and chosen for production. |
Kodak solved its sticking problem in the mold for film cartridge caps by
replacing a 120 stainless steel core with one of a TiN-coated copper alloy and reduced
cycle time as well. |
The Bottom
Line
In the end, Kodak not only reduced average part ejection temperature and eliminated pulled
centers, but decreased the cycle time as well. The 16 percent savings in cycle time and
temperature allowed Kodak to produce 366,100 more 35-mm covers each week with a more
durable and reliable core material.--Jeff Sloan
Injection Molding Magazine
Reprinted with permission |
SITE INDEX
|
Disclaimer
While the information contained is deemed reliable, no warranties are expressed or
implied. For specific information regarding an application please call 1-800-272-3031 or
e-mail us at sales@moldstar.com
|
|
Copyright © 1998-2014 by Performance Alloys &
Services, Inc
Web site hosted by APLUS Hosting
All Rights Reserved.
|